Geomechanical Musings
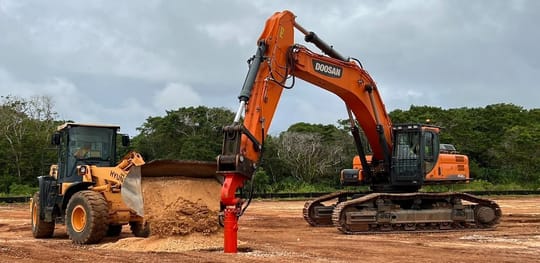
Any method that we deploy to solve engineering problems is an engineering tool. This is a note about the importance of trust while solving difficult design and construction challenges. I’ve always aspired to the role of “Trusted Advisor.” The less-bragadocious “Chief Engineer” was a bar I could clear more consistently, so I put that onaaa
ReadWhen will we see the Stimulus?By:Doug Schwarm On: June 18, 2020Infrastructure stimulus projects will almost certainly be part of our economic recovery. Continuing our conversation about Pandemic Strategy, this article focuses on the likely stimulus rollout schedule and, during the interlude, what strategic actions we should take to prepare. Success happens so often to whomever is standing in the right place at the right time. Opportunity knocks andaaa
ReadHow will you invest your lull?By:Doug Schwarm On: March 18, 2020This is a message of optimism and hope, of an opportunity long awaited that is finally set to arrive. But you need to read to the end to get to the positive, encouraging part. The next two paragraphs are not comforting at all. If you are already feeling redlined trying to chart a course foraaa
ReadThe Future of Utility ProtectionBy:Doug Schwarm On: August 19, 2019Each of us has at least one hilarious-yet-costly story about hitting an underground utility. The one I can contribute is from 1990 and lacks drama, so I mostly tell other people’s stories. Popping the water main in freezing Gillette, Wyoming on the Wednesday before Thanksgiving is a popular one. So is that one time theaaa
ReadWalking our Random PathsBy:Doug Schwarm On: May 26, 2019I have recommended this book to many of you. It was pivotal for my career and yet is specifically not a self-help book. It is filled with facts and observations, but has no advice or recommendations. It sets up the problem; the solution is left to the reader. The title is just a colorful referenceaaa
ReadNeat and SquareBy:Doug Schwarm On: May 17, 2019The best children’s story is Mike Mulligan and his Steam Shovel. About this there can be no debate. It was my favorite story growing up, and it remains pertinent to my work today. You dads and moms can get a copy here: Mike Mulligan and Mary Anne You’re welcome. It’s about a hardworking owner-operator namedaaa
ReadGeotechnical FolkloreBy:Doug Schwarm On: May 5, 2019The Atlas Geotechnical crew is privileged to work all over the world, collaborating with squared-away engineers of varied backgrounds and sharing stories that range from tall tales to practical advice. I’ve learned that every community includes at least a little folklore in how they design and build. Always there is some inexplicable local practice, uniqueaaa
ReadSolving a ProblemBy:Doug Schwarm On: April 30, 2019We’ve got a particularly interesting problem on our desks here at Atlas Geotechnical. There’s a lot at risk, various stakeholders are frustrated with and suspicious of each other, and there’s not enough time. While working this problem through to a pretty tidy conclusion this afternoon, it occurred to me to share the process that weaaa
Read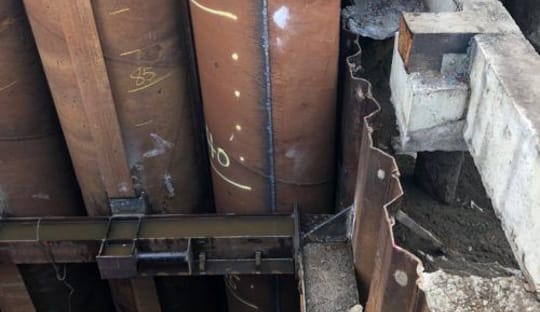
One of our projects achieved a significant milestone on Friday, exactly according to plan. Like most of our projects, it’s interesting construction at a unique site, and there’s no similar recent project to guide design and construction. We learned recently that the shoring design failed to address a subtle but important detail. Once it wasaaa
ReadKilling the HydraBy:Doug Schwarm On: February 18, 20192019 started strongly here at Atlas Geotechnical, but almost immediately we found ourselves overwhelmed re-working problems that we thought we had solved. And that re-work distracted us from other commitments, to the point where we nearly landed on one of our project’s critical paths. And of course when we’re working faster than we should smallaaa
Read