Each of us has at least one hilarious-yet-costly story about hitting an underground utility. The one I can contribute is from 1990 and lacks drama, so I mostly tell other people’s stories. Popping the water main in freezing Gillette, Wyoming on the Wednesday before Thanksgiving is a popular one. So is that one time the CPT rig successfully located the refinery’s hot crude feed. And I like to tell the one about the train that broke the gas pipeline and burned down the bridge even though there’s no drill rig involved. The best stories feature spectacular property damage and a complete absence of injuries or fatalities. In reality though, many of these stories do involve injuries or fatalities. They happen, and we know about them, but we don’t tell them. Despite our lighthearted anecdotes, underground utility protection is serious business. Deadly serious.
A recently completed project for our oldest Pacific Northwest client got us thinking about current practices and developing trends in utility protection. Fewer incidents is everyone’s shared goal. This post organizes some of our thinking about how engineers can protect critical underground infrastructure, and keep everyone safe on the job.
Call Before You Dig
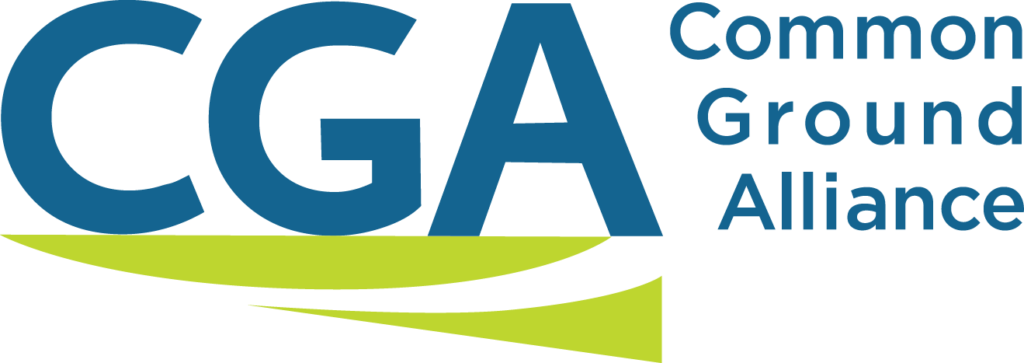
We’re all familiar with 1-call notification requirements, the white-paint-and-a-phone-call exercise we all perform before drilling. Sometimes the engineer and the operator meet up at the site for a chat. But I’m surprised at how few engineers know that a Washington DC based group called the Common Ground Alliance is responsible for publishing the Best Practices Guidelines. In these Guidelines, a1-call notification program is a very small component, and there’s a lot more great guidance available. Common Ground’s current guide contains vast amounts of useful information for operators, engineers, and contractors. The subtitle is “the definitive guide for underground safety and damage prevention,” and it’s not an exaggeration. I highly recommend that you browse through the other parts of the manual and pick some topics for your next staff meeting. Our topic will be Section 5.19, the Excavation Tolerance Zone.
The Gold Shovel Standard
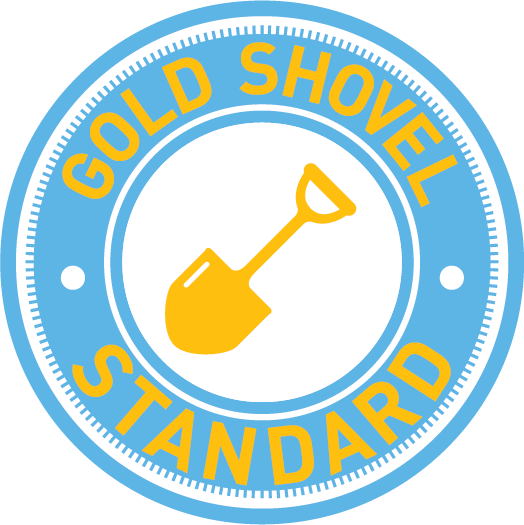
The Gold Shovel Standard (GSS) is a related industry best practices group working to reduce line strikes. GSS member firms adhere to the Common Ground Best Practices, so the groups overlap a little and have complementary objectives. Pacific Gas & Electric founded the group as part of their effort to reduce line strikes down from the high in 2011. This presentation describes how they reduced dig-ins by 38% over less than 3 years.
Right now the GSS is recruiting municipalities to join the Association and start requiring excavation contractors to be Gold Shovel Standard members. Sacramento embraced this practice and enjoyed immediate success. There’s no doubt in my mind that larger municipalities and State DoT’s will soon require GSS membership in their IDIQ geotechnical services contracts. It’s coming (and it’s a good idea anyway) so we might as well get out ahead of the issue if we can.
Developing Practices
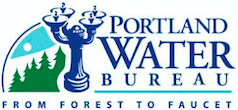
The GSS’s most interesting initiative, to me, is standardizing incident reporting. Standardized data allows statistical analysis. Analyses reveal trends. And trends allows fact-based improvements to best practices. The work of collecting data, analyzing it, and improving practices defines the very kernel of engineering; it’s how the building code came to be and continues to evolve. The GSS is performing foundational work that will lead to standard methods that address utility protection in the same way that ASCE 7 addresses earthquake design.
The Portland Water Bureau’s Utility Protection Plan program may represent the future of excavation planning. It extends water main protection beyond line-strike avoidance to consider structural integrity. For critical water mains the UPP program requires a math-based, drawn, reviewed, and approved plan for supporting the pipe in the excavation. No longer are we allowed to just open up the street, expose the main, and figure out a plan based on what we see. The UPP manual offers some excellent temporary support examples for a variety of crossing geometries. The Portland BWS has expert knowledge of water pipe vulnerability, and their move to require a detailed UPP’s is evidence that good support planning is critical to digging around buried lines.
Most of the Common Ground, GSS, and UPP practices are familiar to us from work around oil and gas pipelines. Pipeline operators, generally acting individually, have each developed practical risk-reduction standard procedures for working around their lines. Adopting these practices reduces risk, improves operational reliability, and saves money. Further, some of North America’s largest General Contractors self-impose extra requirements on their high-risk excavations. These programs yield significant return on investment; they’re good ideas that smart operators embrace. We expect that in the next 3 years, especially as the GSS program gains traction, utility protection will have increasing importance to Atlas Geotechnical’s client base.
Drop us a note if your organization is thinking about adopting the Gold Shovel Standard, incorporating Utility Protection Plans in your internal excavation manual, or just generally interested in improving operations by making better plans. We love these types of conversations.
Interested in getting articles like these sent to your inbox? Sign up for our mailing list here.